Product Description
low flow high torque hydraulic motor 14teeth spline shaft
This series of motor,with its shell made of ductile cast iron of adequate intensity, can be applied to situations with less load and interval operation, widely to agriculture, forestry, plastics, machine tools and min machines, such as the CZPT height adjustment of the injection molding machine, the cleaner, the saw the worktable etc.
CHARACTERISTICS
1 The output shaft, with the deep groove ball bearing, can bear certain axial force and radial force.
2 With the axial oil distribution structur, it is of smaller size and less weight.
3 With 2 inner check valves, no drain connection.
4 With cycoid group with the roller, it has a small friction nd high mechanical efficiency.
TECHNICAL DATA
TYPE
|
BMH-200
|
BMH-250
|
BMH-315
|
BMH-400
|
BMH-500
|
(ml/r) Displacement
|
203
|
253.7
|
318.9
|
405.9
|
471.1
|
Max.Pressure.Drop(Mpa)
|
cont.
|
15.5
|
15.5
|
13.5
|
10.5
|
8.5
|
int.
|
17.5
|
17.5
|
15.5
|
12.5
|
10
|
peak.
|
20
|
20
|
19
|
15.5
|
13
|
Max.Torque(N.m)
|
cont.
|
419
|
493
|
541
|
535
|
541
|
int.
|
473
|
557
|
621
|
636
|
637
|
peak.
|
541
|
636
|
762
|
789
|
778
|
()Speed.Range(cont.)(r/min)
|
370
|
295
|
235
|
185
|
155
|
()Max.Flow(cont.)(L/min)
|
75
|
75
|
75
|
75
|
75
|
()Max.Output.Power(cont.)(Kw)
|
14
|
12.5
|
12.5
|
10
|
8.5
|
Weight(kg)
|
10.5
|
11
|
11.5
|
12.5
|
13
|
Model No.: |
Bmh |
Feature: |
Replace Danfoss Omh, M+S Mh |
Size: |
200ml/R, 250ml/R, 315ml/R, 400ml/R, 750ml/R |
Feature 2: |
High Torque |
Feature 3: |
China Top Quality |
Quality: |
N (AA), G (AAA) |
###
###
TYPE
|
BMH-200
|
BMH-250
|
BMH-315
|
BMH-400
|
BMH-500
|
(ml/r) Displacement
|
203
|
253.7
|
318.9
|
405.9
|
471.1
|
Max.Pressure.Drop(Mpa)
|
cont.
|
15.5
|
15.5
|
13.5
|
10.5
|
8.5
|
int.
|
17.5
|
17.5
|
15.5
|
12.5
|
10
|
peak.
|
20
|
20
|
19
|
15.5
|
13
|
Max.Torque(N.m)
|
cont.
|
419
|
493
|
541
|
535
|
541
|
int.
|
473
|
557
|
621
|
636
|
637
|
peak.
|
541
|
636
|
762
|
789
|
778
|
()Speed.Range(cont.)(r/min)
|
370
|
295
|
235
|
185
|
155
|
()Max.Flow(cont.)(L/min)
|
75
|
75
|
75
|
75
|
75
|
()Max.Output.Power(cont.)(Kw)
|
14
|
12.5
|
12.5
|
10
|
8.5
|
Weight(kg)
|
10.5
|
11
|
11.5
|
12.5
|
13
|
Model No.: |
Bmh |
Feature: |
Replace Danfoss Omh, M+S Mh |
Size: |
200ml/R, 250ml/R, 315ml/R, 400ml/R, 750ml/R |
Feature 2: |
High Torque |
Feature 3: |
China Top Quality |
Quality: |
N (AA), G (AAA) |
###
###
TYPE
|
BMH-200
|
BMH-250
|
BMH-315
|
BMH-400
|
BMH-500
|
(ml/r) Displacement
|
203
|
253.7
|
318.9
|
405.9
|
471.1
|
Max.Pressure.Drop(Mpa)
|
cont.
|
15.5
|
15.5
|
13.5
|
10.5
|
8.5
|
int.
|
17.5
|
17.5
|
15.5
|
12.5
|
10
|
peak.
|
20
|
20
|
19
|
15.5
|
13
|
Max.Torque(N.m)
|
cont.
|
419
|
493
|
541
|
535
|
541
|
int.
|
473
|
557
|
621
|
636
|
637
|
peak.
|
541
|
636
|
762
|
789
|
778
|
()Speed.Range(cont.)(r/min)
|
370
|
295
|
235
|
185
|
155
|
()Max.Flow(cont.)(L/min)
|
75
|
75
|
75
|
75
|
75
|
()Max.Output.Power(cont.)(Kw)
|
14
|
12.5
|
12.5
|
10
|
8.5
|
Weight(kg)
|
10.5
|
11
|
11.5
|
12.5
|
13
|
How to Calculate Stiffness, Centering Force, Wear and Fatigue Failure of Spline Couplings
There are various types of spline couplings. These couplings have several important properties. These properties are: Stiffness, Involute splines, Misalignment, Wear and fatigue failure. To understand how these characteristics relate to spline couplings, read this article. It will give you the necessary knowledge to determine which type of coupling best suits your needs. Keeping in mind that spline couplings are usually spherical in shape, they are made of steel.
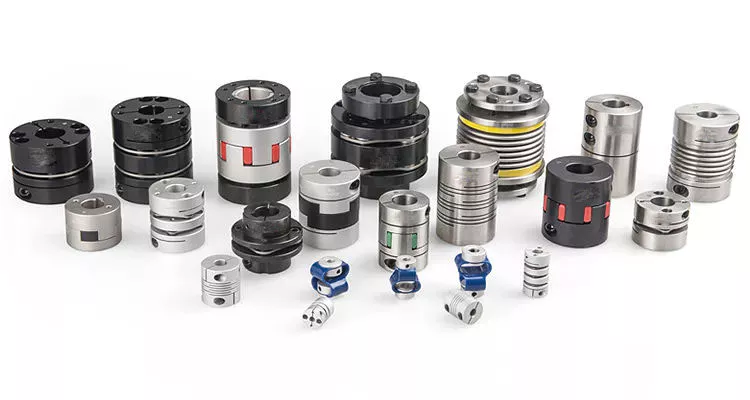
Involute splines
An effective side interference condition minimizes gear misalignment. When two splines are coupled with no spline misalignment, the maximum tensile root stress shifts to the left by five mm. A linear lead variation, which results from multiple connections along the length of the spline contact, increases the effective clearance or interference by a given percentage. This type of misalignment is undesirable for coupling high-speed equipment.
Involute splines are often used in gearboxes. These splines transmit high torque, and are better able to distribute load among multiple teeth throughout the coupling circumference. The involute profile and lead errors are related to the spacing between spline teeth and keyways. For coupling applications, industry practices use splines with 25 to fifty-percent of spline teeth engaged. This load distribution is more uniform than that of conventional single-key couplings.
To determine the optimal tooth engagement for an involved spline coupling, Xiangzhen Xue and colleagues used a computer model to simulate the stress applied to the splines. The results from this study showed that a “permissible” Ruiz parameter should be used in coupling. By predicting the amount of wear and tear on a crowned spline, the researchers could accurately predict how much damage the components will sustain during the coupling process.
There are several ways to determine the optimal pressure angle for an involute spline. Involute splines are commonly measured using a pressure angle of 30 degrees. Similar to gears, involute splines are typically tested through a measurement over pins. This involves inserting specific-sized wires between gear teeth and measuring the distance between them. This method can tell whether the gear has a proper tooth profile.
The spline system shown in Figure 1 illustrates a vibration model. This simulation allows the user to understand how involute splines are used in coupling. The vibration model shows four concentrated mass blocks that represent the prime mover, the internal spline, and the load. It is important to note that the meshing deformation function represents the forces acting on these three components.
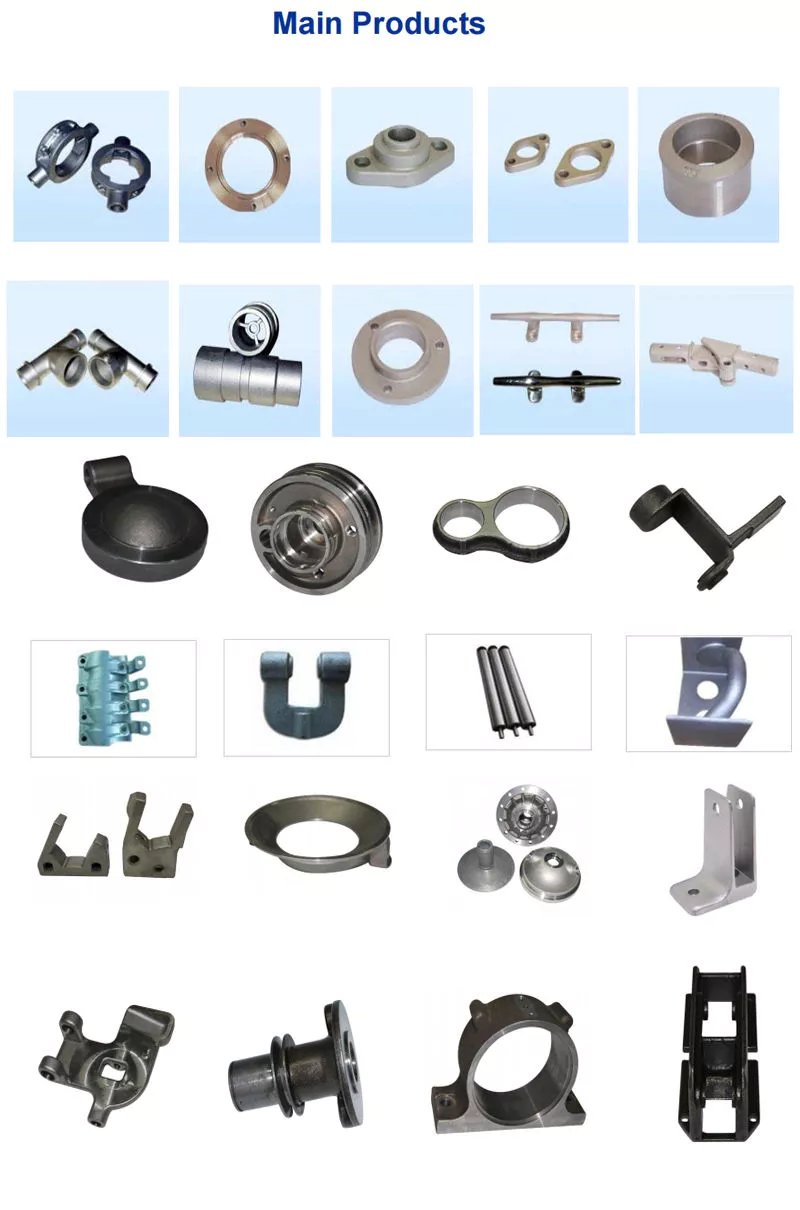
Stiffness of coupling
The calculation of stiffness of a spline coupling involves the measurement of its tooth engagement. In the following, we analyze the stiffness of a spline coupling with various types of teeth using two different methods. Direct inversion and blockwise inversion both reduce CPU time for stiffness calculation. However, they require evaluation submatrices. Here, we discuss the differences between these two methods.
The analytical model for spline couplings is derived in the second section. In the third section, the calculation process is explained in detail. We then validate this model against the FE method. Finally, we discuss the influence of stiffness nonlinearity on the rotor dynamics. Finally, we discuss the advantages and disadvantages of each method. We present a simple yet effective method for estimating the lateral stiffness of spline couplings.
The numerical calculation of the spline coupling is based on the semi-analytical spline load distribution model. This method involves refined contact grids and updating the compliance matrix at each iteration. Hence, it consumes significant computational time. Further, it is difficult to apply this method to the dynamic analysis of a rotor. This method has its own limitations and should be used only when the spline coupling is fully investigated.
The meshing force is the force generated by a misaligned spline coupling. It is related to the spline thickness and the transmitting torque of the rotor. The meshing force is also related to the dynamic vibration displacement. The result obtained from the meshing force analysis is given in Figures 7, 8, and 9.
The analysis presented in this paper aims to investigate the stiffness of spline couplings with a misaligned spline. Although the results of previous studies were accurate, some issues remained. For example, the misalignment of the spline may cause contact damages. The aim of this article is to investigate the problems associated with misaligned spline couplings and propose an analytical approach for estimating the contact pressure in a spline connection. We also compare our results to those obtained by pure numerical approaches.
Misalignment
To determine the centering force, the effective pressure angle must be known. Using the effective pressure angle, the centering force is calculated based on the maximum axial and radial loads and updated Dudley misalignment factors. The centering force is the maximum axial force that can be transmitted by friction. Several published misalignment factors are also included in the calculation. A new method is presented in this paper that considers the cam effect in the normal force.
In this new method, the stiffness along the spline joint can be integrated to obtain a global stiffness that is applicable to torsional vibration analysis. The stiffness of bearings can also be calculated at given levels of misalignment, allowing for accurate estimation of bearing dimensions. It is advisable to check the stiffness of bearings at all times to ensure that they are properly sized and aligned.
A misalignment in a spline coupling can result in wear or even failure. This is caused by an incorrectly aligned pitch profile. This problem is often overlooked, as the teeth are in contact throughout the involute profile. This causes the load to not be evenly distributed along the contact line. Consequently, it is important to consider the effect of misalignment on the contact force on the teeth of the spline coupling.
The centre of the male spline in Figure 2 is superposed on the female spline. The alignment meshing distances are also identical. Hence, the meshing force curves will change according to the dynamic vibration displacement. It is necessary to know the parameters of a spline coupling before implementing it. In this paper, the model for misalignment is presented for spline couplings and the related parameters.
Using a self-made spline coupling test rig, the effects of misalignment on a spline coupling are studied. In contrast to the typical spline coupling, misalignment in a spline coupling causes fretting wear at a specific position on the tooth surface. This is a leading cause of failure in these types of couplings.
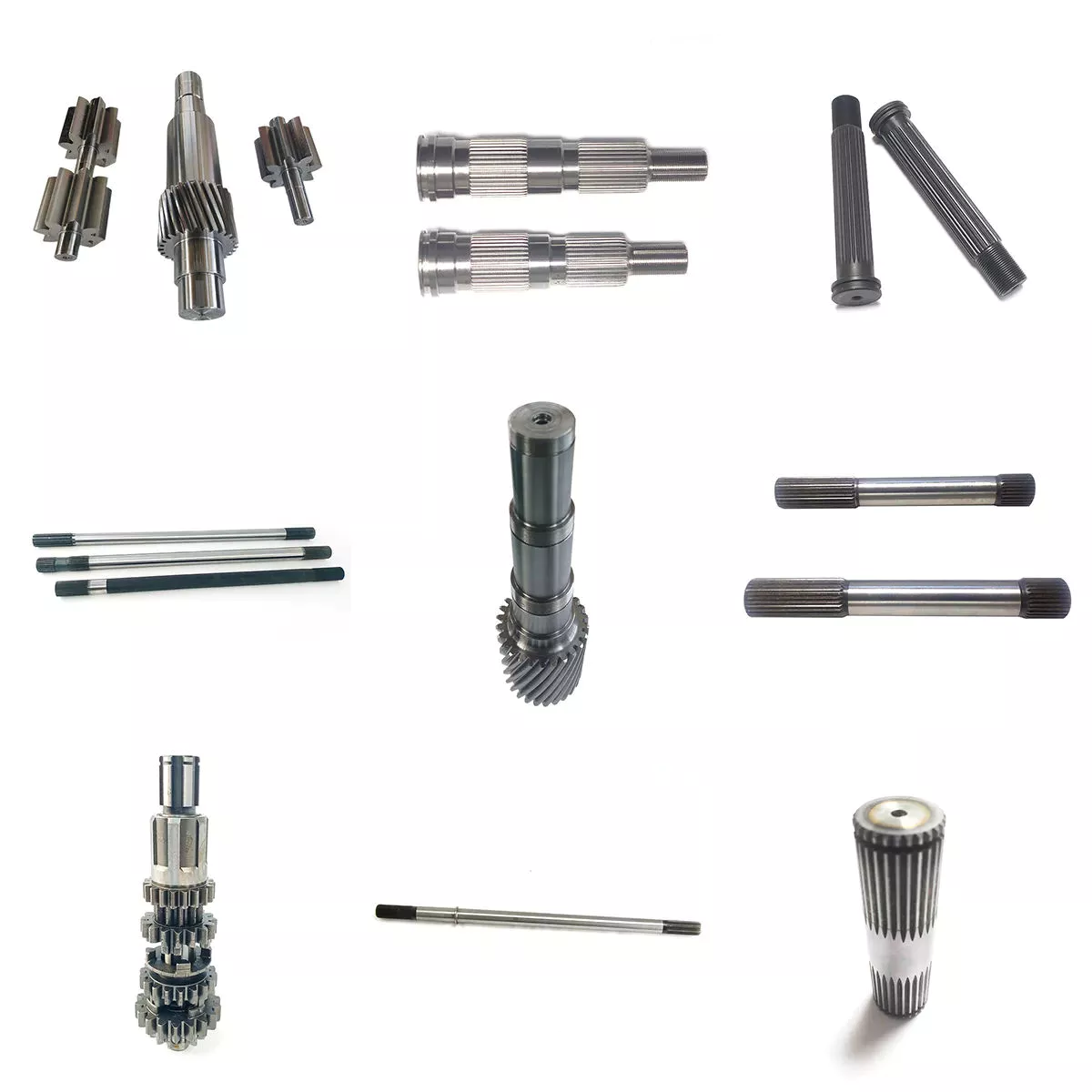
Wear and fatigue failure
The failure of a spline coupling due to wear and fatigue is determined by the first occurrence of tooth wear and shaft misalignment. Standard design methods do not account for wear damage and assess the fatigue life with big approximations. Experimental investigations have been conducted to assess wear and fatigue damage in spline couplings. The tests were conducted on a dedicated test rig and special device connected to a standard fatigue machine. The working parameters such as torque, misalignment angle, and axial distance have been varied in order to measure fatigue damage. Over dimensioning has also been assessed.
During fatigue and wear, mechanical sliding takes place between the external and internal splines and results in catastrophic failure. The lack of literature on the wear and fatigue of spline couplings in aero-engines may be due to the lack of data on the coupling’s application. Wear and fatigue failure in splines depends on a number of factors, including the material pair, geometry, and lubrication conditions.
The analysis of spline couplings shows that over-dimensioning is common and leads to different damages in the system. Some of the major damages are wear, fretting, corrosion, and teeth fatigue. Noise problems have also been observed in industrial settings. However, it is difficult to evaluate the contact behavior of spline couplings, and numerical simulations are often hampered by the use of specific codes and the boundary element method.
The failure of a spline gear coupling was caused by fatigue, and the fracture initiated at the bottom corner radius of the keyway. The keyway and splines had been overloaded beyond their yield strength, and significant yielding was observed in the spline gear teeth. A fracture ring of non-standard alloy steel exhibited a sharp corner radius, which was a significant stress raiser.
Several components were studied to determine their life span. These components include the spline shaft, the sealing bolt, and the graphite ring. Each of these components has its own set of design parameters. However, there are similarities in the distributions of these components. Wear and fatigue failure of spline couplings can be attributed to a combination of the three factors. A failure mode is often defined as a non-linear distribution of stresses and strains.


editor by czh 2022-11-30